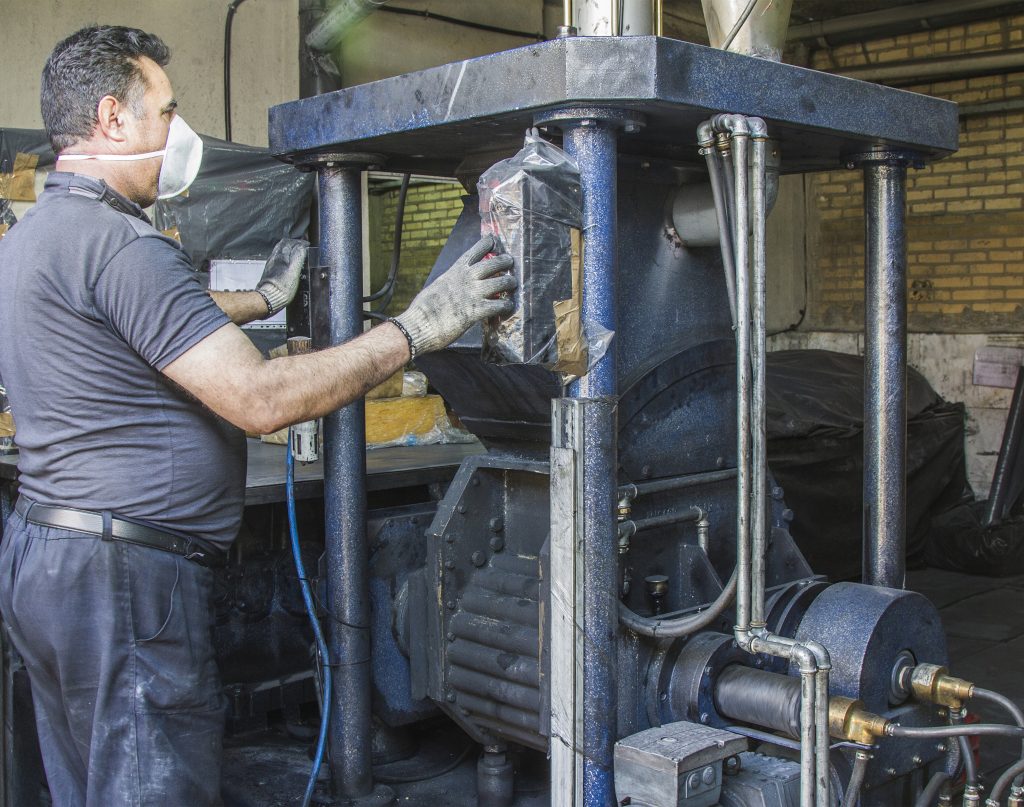
Rubber industry
Rubber has become an important economic and strategic material. Transportation, chemical, electrical and electronics industries, as well as space, are all major consumers of rubber. When the production of natural rubber was stopped due to the Japanese invasion of rubber production areas at the beginning of World War II, the United States began to build synthetic rubber production units, which developed rapidly, so that currently 88% of the rubber consumed in the United States is of synthetic origin. . The rubber industry includes the following: the production of synthetic rubber raw materials, various types of rubber, the import of natural rubber, the production of rubber additives, and finally the manufacture of rubber products.
historical background
Christopher Columbus discovered that Native Americans played with rubber balls. Rubber objects were also recovered from a Maya sacred well in the Yucatan. Rubber, as far as we know, is a product of the American soil, but it has only been developed to this extent through its transportation to the Far East and cultivation there. The name “rubber meaning eraser” was given by Priestley, the discoverer of oxygen, he was the first person to see the ability of rubber to “erase” pencil marks. Rubber materials were the only result of efforts to purify and preserve materials such as styrene, butadiene, and isoprene, which were obtained from the destructive distillation of natural rubber, thus paving the way for the production of synthetic rubber. With the beginning of the First World War, inferior types of rubber from dimethyl butadiene were produced in Germany and Russia. Extensive research during the 1920s led to the discovery of co-emulsification of butadiene and styrene, as well as butadiene and acrylonitrile.
Goodyear became famous by discovering the curing or vulcanization of rubber by sulfur in 1839. This discovery solved the problem of the natural viscosity of rubber and made it commercial. Since then, it has been found that many materials change the speed of this reaction and that some auxiliary materials, with changes in the mixture, provide the possibility of shaping or making rubber parts, which are then stabilized in their final shape by the curing reaction. Historically, the biggest changes have been the result of restrictions on the import of natural rubber to the United States due to the invasion of Japanese forces in 1941. This move led to the research and production of various synthetic rubbers during the later eras.
natural rubber
Countless plants such as dandelion, guayel, mulberry, and American mulberry have been suggested as a source of rubber, but none have succeeded the sap-producing tree Hevea brazilensis, as well as the gum of the sapodilla tree and the balata tree. Natural rubber was produced mainly in plantations in Malaysia, Indonesia, Liberia and their neighbors, probably because they did not have the problems of fungal diseases and insects that threatened native plantations in the Americas. It takes about 7 years for these trees to reach the reproductive age and after that they bear fruit for several years. To obtain the sap, the bark is removed so that the liquid collects in small cups, the cups must be collected regularly to avoid rotting or contamination of the sap. After that, the leachate is taken to the collection point, where it is protected by adding ammonia after filtering. The rubber is separated through a process called coagulation, this is done by adding various acids or salts, during this process, the rubber is separated from the liquid in the form of a white mass of paste, and then it is dried using a sheet roller. The newer method is to convert the coagulated sap into grains by using rotating blades or cutting between two rollers that rotate at different speeds. The seeds are then dried for several hours in a mechanical mite dryer, a process that took several days in the old method that used air or wood smoke for drying. In any case, they make dense dried sheets or seeds and use them to make bales weighing 33 kg. Some of the natural rubber is sold in the form of leachate (which has been placed in a centrifuge after stabilization with concentrated ammonia and up to 60% solid content).
Before the rubber can be mixed with the necessary additives, it must be softened. This is done with a double roller mill (where the rollers rotate at different speeds) or a mixer (where off-center vanes push the rubber against the walls of the mixer). After softening, admixtures such as carbon black (as filler), sulfur or sulfur compounds (for Vulcan9, Vulcan accelerator, protective antioxidant and oil) are added on the same rollers or mixer. Roller mixers are used only in the smallest units. Mixers are very They are large and can handle only a small amount of rubber at a time.An example mixer may be as tall as a two-story building and still handle only 250 kg packages.
After mixing, the rubber is shaped into the desired product by punching or molding and then it is baked. Volcanization results in a cross-linked thermosetting resin that does not soften or melt upon reheating. Accurate control of the vulcan heat (140 or higher) is important to achieve optimal properties in cured rubber. Since volcanism is a chemical process, its speed increases with temperature and care should be taken not to do it prematurely.
Natural rubber or caoutchouc is cis-1,4-polyisoprene and its molecules are crystallized due to stretching, thus providing a desirable form of reinforcement. As a structural prerequisite, the molecules of natural and synthetic rubbers must be long. The characteristic property of reversible elongation is due to the random and coiled arrangement of long chains. Due to the tension, the chains collide, but like a metal, after releasing the tension, they return to their coiled shape. Natural rubber has 6 to 8% non-rubber materials and shows great resistance to heat generation. Table 1 shows monolayers, bilayers or co-polymers of all types of tires.
Synthetic rubber
Synthetic rubbers are classified into vulcanizable and non-vulcanizable groups, this is done through the chemical composition of the polymer chain. Table 2 shows different types and categories of tires along with their accepted abbreviations. The most widely used synthetic rubber is SBR. Other common rubbers include polybutadiene, polyethylene-propylene, butyl rubber, neoprene, nitrile rubber and polyisoprene.
Mixing tires
Rubber (natural or synthetic) usually cannot be used alone. The desired properties of softness, elasticity, toughness, hardness or softness, abrasion resistance, impermeability and thousands of different combinations of properties are provided by the rubber compound. A sample rubber compound is shown in Table 3.
Chemical additives are classified into the following groups depending on their usage (Table 4). Volcanic materials are usually sulfur compounds, which are obtained from their reaction with network materials, and the network connections are of the -C-Sx-C- type. Cross-links may be mono-, di-, or polysulfide. The type of bonding is determined by sulfur concentration, accelerator, inhibitor and temperature. Most of the production conditions of a specific product are experimental, but the scientific basis has been laid to determine the conditions of its volcano. Accelerators are compounds that reduce the time required for rubber vulcanization from hours to minutes. In addition, less sulfur is needed and a more uniform product is obtained. The mechanism of action of the accelerator is not clear despite extensive research, but it is assumed that the activated form of sulfur forms a “sulfur bridge” in the reactive positions of the rubber molecule and creates a hard network by connecting large molecules. Most accelerators contain nitrogen and sulfur.
Anti-aging substances or antioxidants protect rubber parts from oxygen and ozone attack. These compounds are classified as antioxidants, anti-ozone or anti-bending agents. Their action is that they stop radical chain reactions and thus prevent further destruction of the chain. Industrial materials are usually amine or phenolic. Amines are strong preservatives and are widely used in tires and other dark parts (where discoloration or pigmentation is not important). Examples of amine compounds are: alkylated diphenylamine, alkylated or aryl-p-phenyldiamine, reaction products of aromatic amines with aldehydes or quinones. Regarding light-colored parts, alkylated phenol and its derivatives are used to protect the rubber against oxygen with minimal color change.
Catalytic softeners or anti-flocculation agents make the rubber easier to process by reducing its viscosity. When mixed with rubber, they cause the chain to break and naturally decrease the molecular weight. Anti-flocculation agents can be used both in recycling vulcanized rubber and in softening raw materials with high molecular weight. Inert or neutral fillers are added to rubber in large quantities. Some of them are used only to harden or soften the mixture. Others leave a significant effect known as the strengthening effect, which is physical-chemical in nature. Clay, calcium carbonate, coal barite, and almost any solid round can be added to rubber, as a result of which all tensile properties are reduced, but at the same time, price reduction, appropriate hardness, maintaining shape, color and other desirable properties are among its other effects. But the powder of some amorphous materials, especially carbon black and silica, incredibly increases strength, elasticity, wear resistance and other desirable properties, and for this reason, they are known as reinforcers. Processability is improved by using recycled rubber, waxes, oils, factis (vulcanized vegetable oils) and mineral rubbers (asphalt, bitumen and vulcanized unsaturated hydrocarbons) or through chemical reaction on the molecule, mechanical work, heat and grinding. The spongy structure is obtained by adding sodium bicarbonate, ammonium carbonate and bicarbonate, urea or gaseous organic compounds. Hard rubber can be obtained by significantly increasing sulfur and using filler in large quantities.
tire making
As a plastic material, the operation of spreading, gluing, rolling, molding, punching, puttying, forming, coating on fabric, plastic or metal; Sandwiching and sealing can also be done with tires. Rubber is an extremely tough material and requires heavy machinery.
Rolling or coating
One of the most basic uses of tires has been covering fabric to make it waterproof. The solution or rubber putties in solvents can be easily spread on the fabric, but if the necessary materials for curing and controlling the properties are not used, completely unfavorable results will be obtained. To impregnate the fabric with rubber compounds, the rolling method is used, in such a way that the rubber mixture is rolled into the fabric under pressure on multi-cylinder roller machines. Tire yarn is a special item that cotton, rayon, nylon or polyester yarns are attached in a parallel arrangement by rubber on a rolling machine.
molding
Rubber paste compounds can be molded into any shape, and their shape can be stabilized by curing. A good example is a tennis ball. A very high-quality and flexible type of rubber is molded in a mold that is shaped like half a ball. Then they glue this two-piece together (with a pill of a gaseous chemical inside) and bake it (the brain product is a ball), on this brain, fabric and suitable fluffy fibers are glued. This material is a complex structure